Axiom™ IM
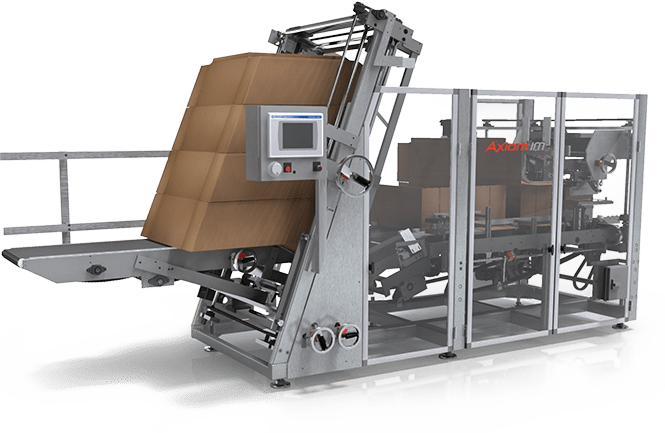
AXIOM IM CASE & TRAY PACKER
High-Speed, Customized Case & Tray Packing
The Axiom IM case packer is the industry-proven workhorse for high-speed, customizable case packing, operating at 45–60 cases per minute with servo-driven precision. Its modular, open-frame design allows for extensive infeed and loading customization, making it the ideal choice for complex pack patterns, wraparound cases, and knockdown designs. Unlike robotic-only solutions, Axiom IM integrates both servo and mechanical innovations to maximize efficiency, flexibility, and reliability. With quick-changeover capabilities and exceptional tolerance for case variability, it excels in demanding, high-volume production environments where speed and adaptability are critical.
products per minute with Velocity II™
cases per minute
installations since 2003
Axiom IM Pack Patterns
The Axiom IM case packer’s servo technology delivers smooth, harmonious performance during case loading, while maintaining accurate handling of complex pack patterns and diverse styles.
Axiom IM Key Features
Automated Changeovers
Automatic adjustment of servo controlled change points make changeovers precise, repeatable and fast, reducing manual adjustments
Accurate Product & Material Control
Improved Ergonomics & Accessibility
Simplified Maintenance
Effortless Adaptability
Meets the most challenging applications, adapting to evolving and uncertain product life cycles, with the ability to reorientate pack patterns multiple times
Customized Product Infeed & Collation
A variety of custom options including inline, right angle or counter flow infeeds address your unique application
Precision Flap Folding
Efficient Case Sealing
Drive
Servo motors
Flight Chains
#2060 chains
Speed
Up to 45 cases/minute;
Product and pack pattern dependent
Product/Package Size Range
Per project specification
Magazine Capacity
6′ (1829 mm);
8 blanks per inch
Frame/Finish
Powder-coated cold-rolled steel; optional stainless steel frame. All parts in contact with product are stainless steel, anodized aluminum and plastic OEM parts with manufacturer’s standard finish.
Glue System
Nordson ProBlue® Flex
Flap Closing & Compression
Servo motors
Adjustments
Threaded screws, handwheels and hand knobs with position pointers and scales; Digital scales, phase adjustments and recipe control of servo motions and glue (optional)
Safety
Guarded for current OSHA standards; Clear sightlines through and around machine; Respect one-meter-reach rule
Electrical
Allen Bradley motion/logic control, PanelView, NEMA12 wiring and enclosures; NEMA 4/4X wiring and enclosures (optional); Washdown options available for stainless steel frame upgrade
Power
480 V, 50/60 HZ, 3 PH
Air
90 PSI (6.2 bar)
Buy with confidence. Experience the difference.
Douglas stands behind our equipment with a 3-year limited component and limited lifetime frame warranty.