Case & Tray Packer
This Simplifies Everything.
To develop the patent-pending CpONE® Intermittent Motion Case Packer, we leaned on new technology and 55+ years of product and material control experience. The result is next-level simplicity. The CpONE leverages the development of more advanced mechanisms and engineered motion control. It smartly applies these advancements to improve machine usability and uptime. A key enabler developed into the heart of the machine is the robotic arms. These highly engineered arms are applied based on application need, with full deployment including arms controlling the case setup, loading and sealing sections of the machine. The scalability of the CpONE platform allows it to address different application, speed and investment levels. The CpONE represents a step-change in simplicity and usability while maintaining reliability and proven performance. Simple operation. Simple maintenance. Simply next-level performance.The resulting main machine configurations offer up to:
40% fewer parts
30-50% fewer lubrication points
40% fewer change points
Speeds: 5 cases/minute up to 45 cases/minute
Changeover Features Simplify and Reduce Changeover Time
- Up to a 40% reduction in changeover points on the main machine
- Magazine bed and compression section height adjustments are eliminated by robot and mechanism flexibility
- Standard automatic adjustment of flap trap location, load funnel width, manufacturer’s glue nozzle height and centerline height of minor flap guides and major flap glue nozzles; additional automatic changeover points available as options
- Accessibility and ease of making manual adjustments
- Forming die case setup for wraparound cases is more tolerant of variations in corrugated materials
- Pivoting major flap folding and compression with 8-corner case squaring for a quality finished product
- Heightened visibility and ergonomic accessibility
- Scalable drive platforms using servo motors and servo-pneumatics; or all servo motors
- Robot arms, applied based on application, greatly reduce the number of bearings, linear bearings, belts, pulleys, tensioners, cable tracks, grease points and framework resulting in up to 40% fewer parts to maintain
- Rockwell drives, HMI and Logix controller (no additional controllers)
- Electronic ‘hand wheel’ jog function provides incremental jogging to set up or diagnose timing and material changes
- Added convenience features such as pivoting glue gun mounts provide easy access for maintaining glue nozzles
- Sanitary design
- Three-year limited warranty coverage of major machine components
Operation
Consolidated functions
40% fewer change points
Scalability
Available technologies scale the machine to suit application and specification requirements
Accessibility
Main robot functions overhead
50% reduced machine volume
Ergonomics
Low-profile robots and mechanisms ease access
Up to 40% fewer parts in the main machine
Maintenance
Simplified machine design
Fewer lubrication points
Cleanliness
Hygienic frame design
Minimal horizontal surfaces
Simplified access, enhanced functionality and standard automated change points offer substantial improvements in changeover speed and accuracy.
Change points eliminate up to 40% of manual adjustments including:
Magazine bed height adjustment
Flap traps and adjustments for most applications
Case compression height adjustment
Load funnel width
Manufacturer’s joint glue gun height
Flap glue gun heights
Minor flap containment guides
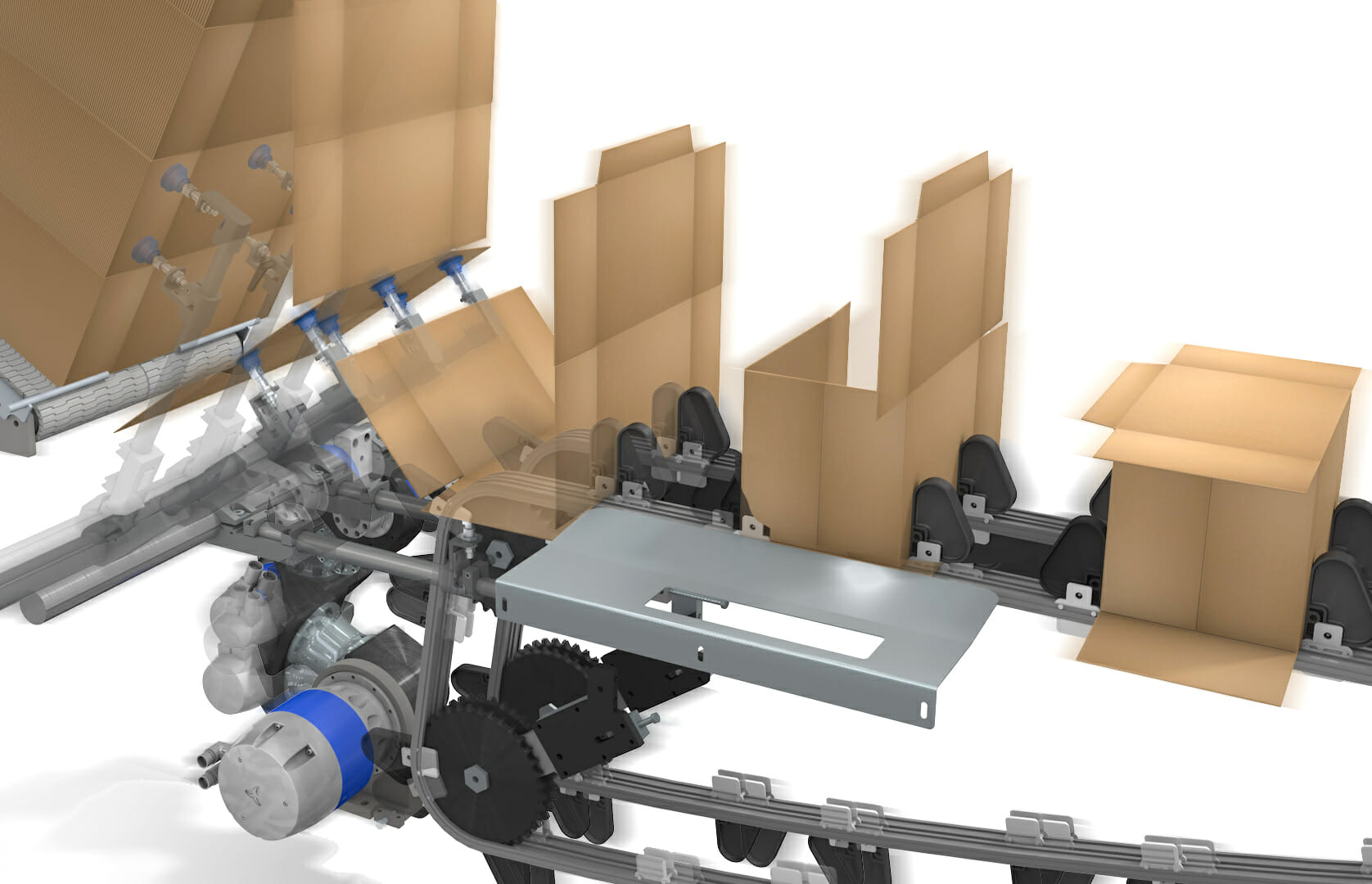
- Leverages the ‘in-motion’ segment of indexing to optimize case setup
- Case setup motion recipes set via HMI using basic case dimension parameters
- Improves efficiency and dramatically reduces disruptive forces in erecting and controlling the case
- Separate flap traps eliminated on small to mid-size case applications
- Enables more consistent glue application and reduced consumption
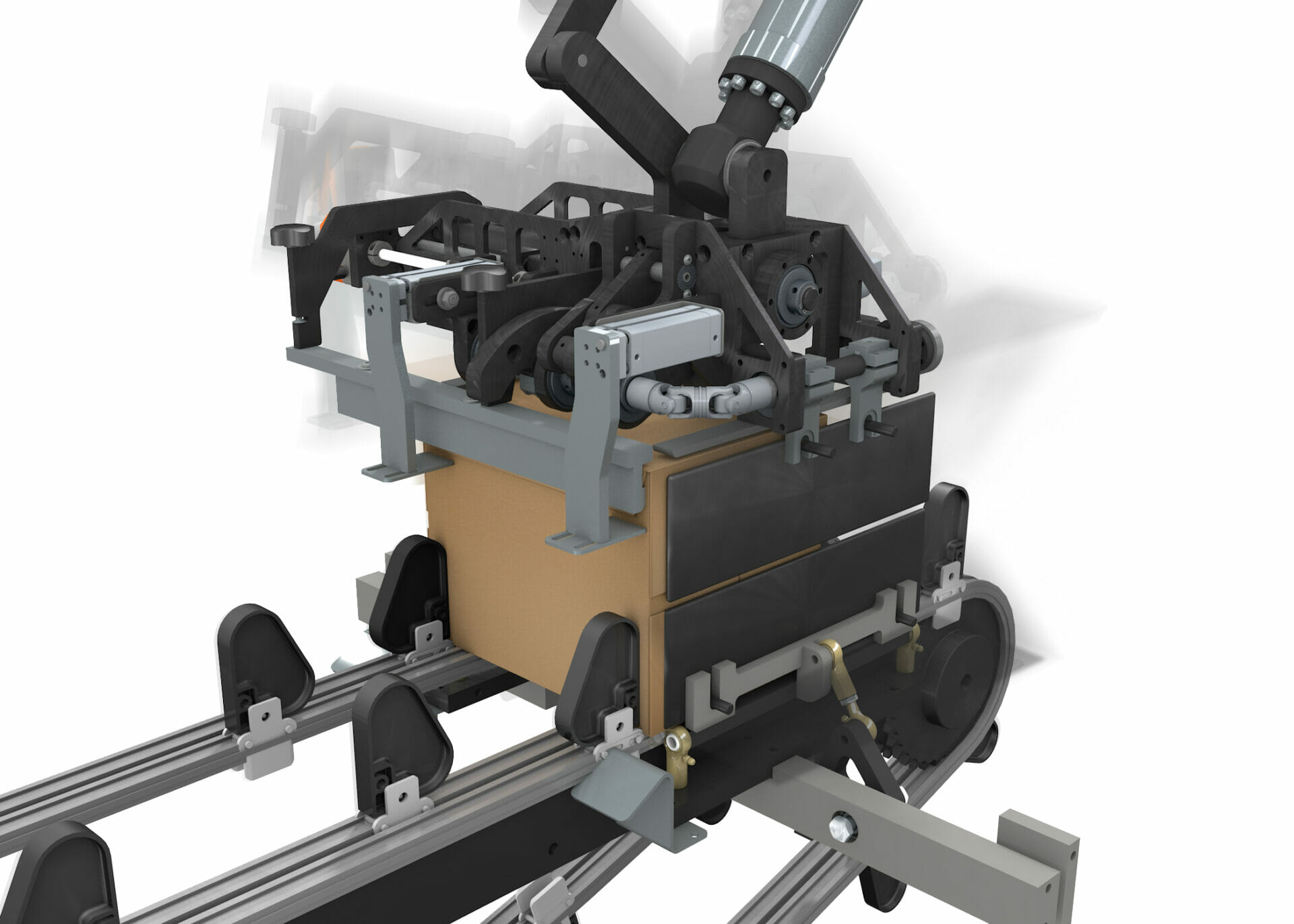
- 8 corner case squaring optimizes case form
- Pivoting major flap folding and sealing ensures consistency
COLLATING & LOADING
Velocity™ II High Speed Stacker – Gently forms stacked product patterns without interruption, providing continuous product flow at speeds up to 600 products per minute. Patented techniques include an increased flexibility for running different product heights while still providing tool-less changeovers with an intuitive HMI control panel.
Pick and Place – Ideal for products such as tapered cups that cannot be pushed one against the other. A variety of vacuum or mechanical techniques are used, depending on the application.
Raise on Return Loading – This high speed loading technique starts to accumulate product for the next pack pattern as soon as the loader clears the accumulation section.
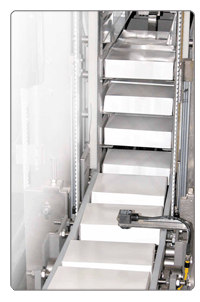
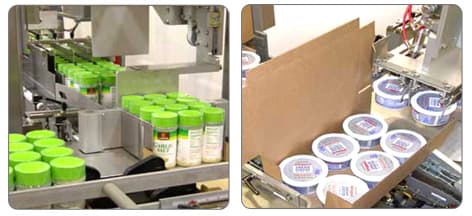
PRODUCT HANDLING
A variety of advanced infeed solutions are offered to optimize performance for specific product types while maintaining gentle product handling to ensure highest package integrity. Some commonly used systems include:
Servo Lane Mergers and Dividers – Perfect for applications where any shape or sized product cannot be flood or mass fed. A fixed number of products are smoothly fed to metering systems, where balanced product lanes are required.
Recirculating Conveyor – A complete recirculating loop system that controls product population and reduces line pressure as products are distributed into lanes.
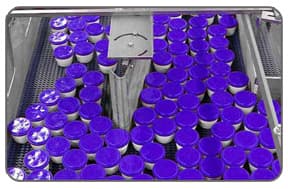
Fast, repeatable changeover feature offers multiple enhancements.
Changeover time – significantly reduces time to less than 5 minutes (time of changeover is dependent on extent of changeover)
Repeatability – rail positions are recipe-driven and locked in place to within +/- 1/32″
Flexibility – ability to place lanes where desired as opposed to centerline or fixed side adjustments and more customer options for generating product-specific recipes
Durability – infeed rail’s holding force can withstand high product pressure
Ergonomics – minimizing manual adjustments maximizes efficiency and promotes safety in the work environment
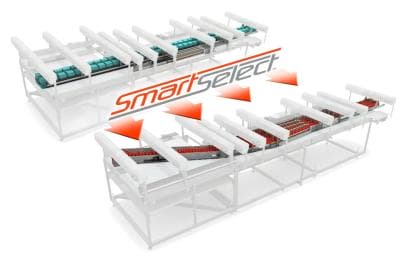
Speeds: | 5 cases/min to 45 cases/min, scalable configurations address different application, speed and investment levels |
Case Types: | Wraparound cases, knockdown cases and trays RSC, HSC, economy, harness, POL and FOL flap configurations Minimum flaps: 2″ (50.8 mm) Maximum flaps: 6″ (152.4 mm) Minimum manufacturer’s flap for wraparound cases: 1.5″ (38.1 mm) (outside manufacturer’s flap standard, inside optional) |
Case Size Range: | Direction of Travel x Vertical x Across Machine* CpONE – 18″ index (457.2 mm) Minimum: 4″ (101.6 mm) x 3″ (76.2 mm) x 6″ (152.4 mm) Maximum: 12″ (304.8 mm) x 12″ (304.8 mm) x 18″ or 22″ (558.8 mm) CpONE – 24″ index (609.6 mm) Minimum: 4″ (101.6 mm) x 3″ (76.2 mm) x 6″ (152.4 mm) Maximum: 18″ (457.2 mm) x 12″ (304.8 mm) x 18″ or 22″ (558.8 mm) *Maximums may not be available in combination – larger format capabilities available |
Frame/Finish: | Powder-coated cold rolled bar stock, sheet, and tubular steel Gray metallic, DuPont 616 Washdown options available |
Magazine Capacity: | 6′ (1829 mm) |
Glue System: | Nordson ProBlue® |
Adjustments: | HMI selectable recipes, automatic position actuators, threaded screws, hand wheels and hand knobs with position pointers and numeric scales |
Guarding: | Category 3 guarding Full length 1/2″ (12.7 mm) acrylic guard doors (main machine) and clear polycarbonate |
Electrical: | Rockwell Automation (AB) programmable logic controller, servo and AC drives, and PanelView+ HMI Servo motors – Rockwell VPL and Wittenstein TPM NEMA 12 wiring and enclosures, floor mounted, overhead mounted optional Washdown options available |
Power: | 480V, 50/60HZ, 3PH Second 480V drop down for glue unit |
Air: | 90 PSI (6.2 bar) |
Elegant use of technologies and components, along with product and package flexibility, the CpONE® stands ready to be the solution of choice for many applications.
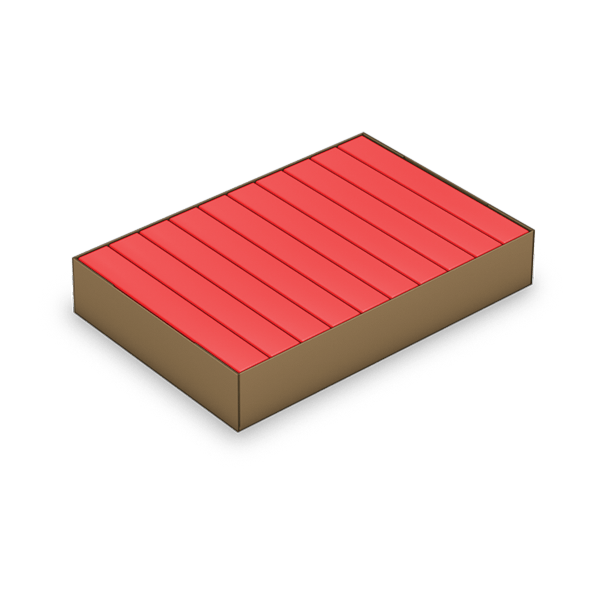

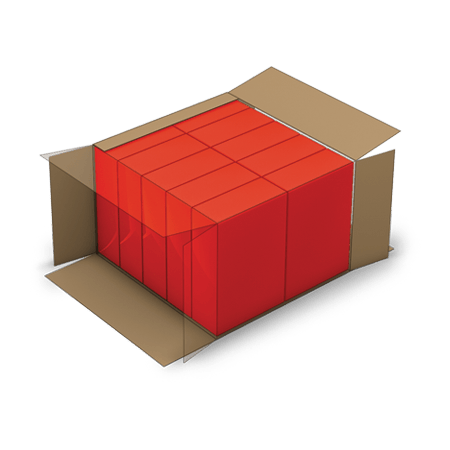
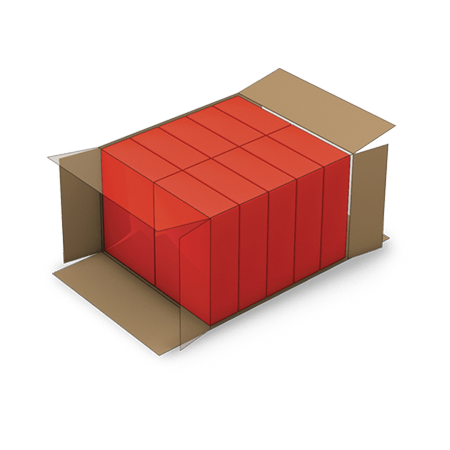
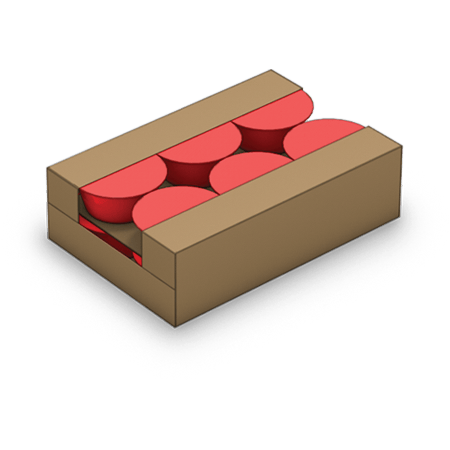
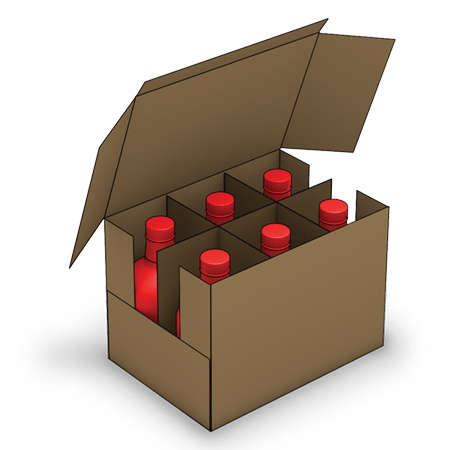
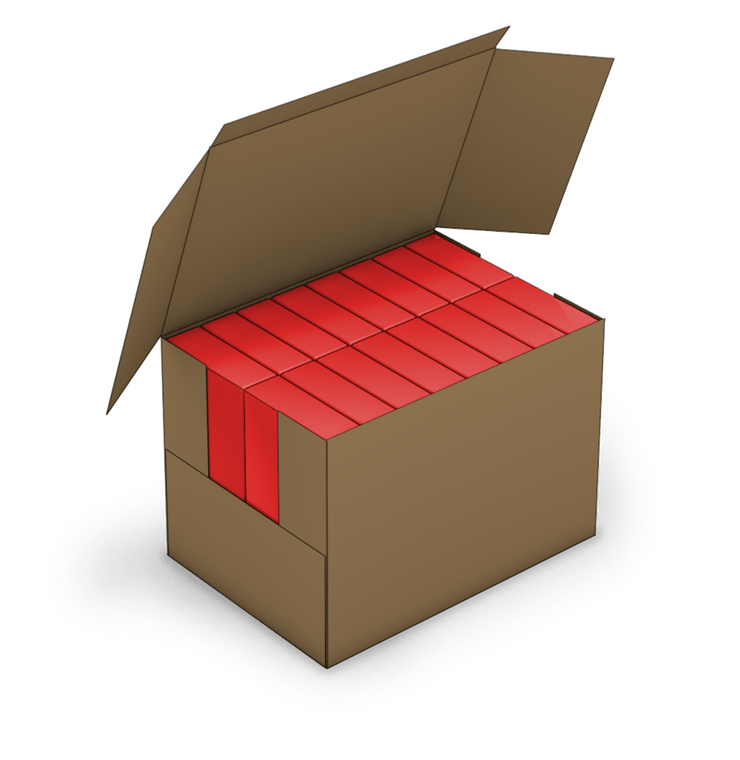
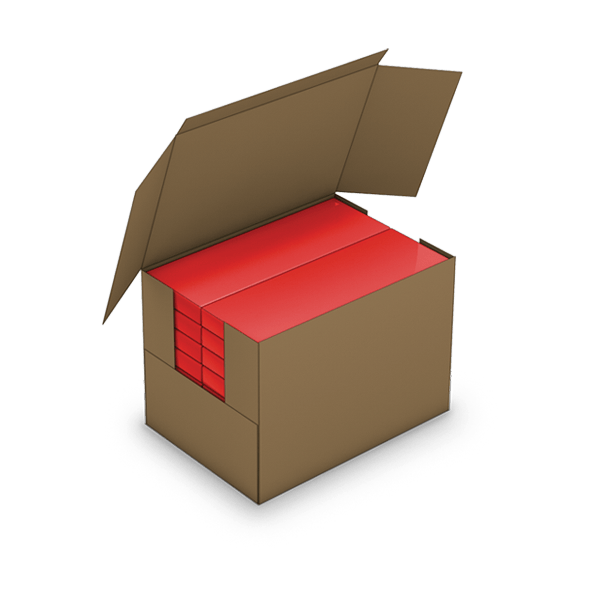